Ein dynamisches Werk mit den besten, modernsten und effizientesten Verfahren.
Die Gießerei SCM ist in der Lage, Gussteile mit variablen Abmessungen bis zu 2.500 x 2.500 x 1.200 mm und einem Gewicht von 150 bis 4.500 kg herzustellen. Das Unternehmen verfügt über eine besondere Kompetenz für die Produktion von kleinen und mittleren Serien, Prototypen und Einzelstücken.
SCM produziert fast alle Kerne mit einem Gewicht von wenigen Kilo bis zu 2 Tonnen, und gewährleistet dadurch eine vollständige Prozesskontrolle bei der Herstellung von Gussteilen mit hohem technischem Anspruch, die sich auch durch äußerst komplexe Geometrien auszeichnen.
ANLAGEN MIT MODERNSTER HOCHTECHNOLOGIE
Formanlage No-Bake
Mit demPhenol-Furan-Harz-Verfahren, das mit 1 Mischer von 30 Tonnen / h ausgestattet ist, wird die Produktion mit 95% regeneriertem Sand ausgeführt.
Komplett mechanische Lackier-, Verzweigungs- und Trocknungslinie mit einer stündlichen Produktion von 10 Bügeln pro Stunde für serienmäßige Flasks.
Zwei ausgestattete Bereiche für die Produktion von großen Gussteilen und für die Produktion von Teilen mit komplexen Kernbaugruppen.
Die Anlage unterliegt ständig Aktualisierungen, Modifikationen und Anpassungen, die auch von Kundenwünschen vorgegeben werden.
Die Nachgusslinie wurde 2012 vollständig mechanisiert, und in diesem Zusammenhang wurden alle manuellen Arbeitsvorgänge eliminiert. Insbesondere ist ein automatischer Abtrenner vorhanden, der von einem Clansmann-Manipulator mit einer Kapazität von 4000 kg bedient wird, und mit der Strahlanlage verbunden ist, die ebenfalls von einem Clansmann-Manipulator mit einer Kapazität von 3000 kg bedient wird.
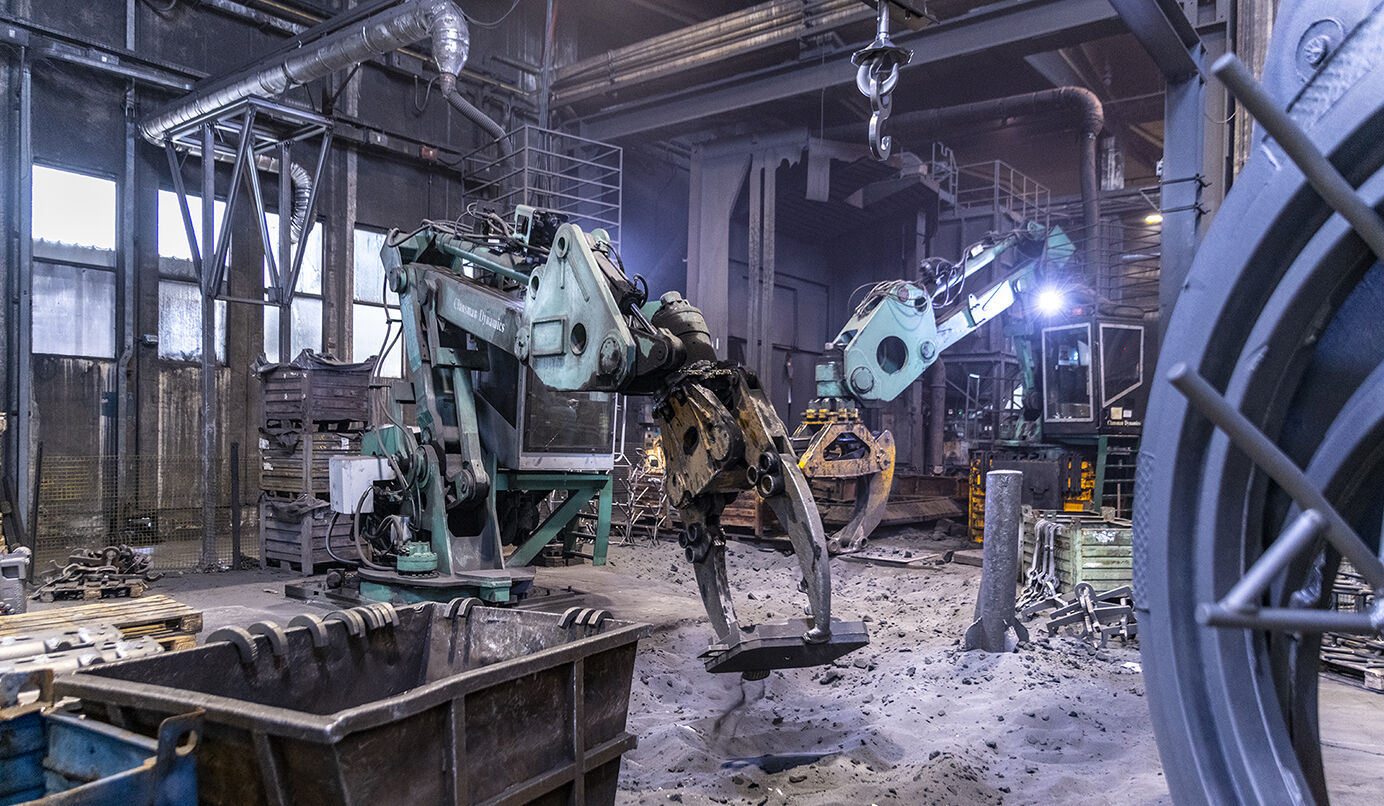
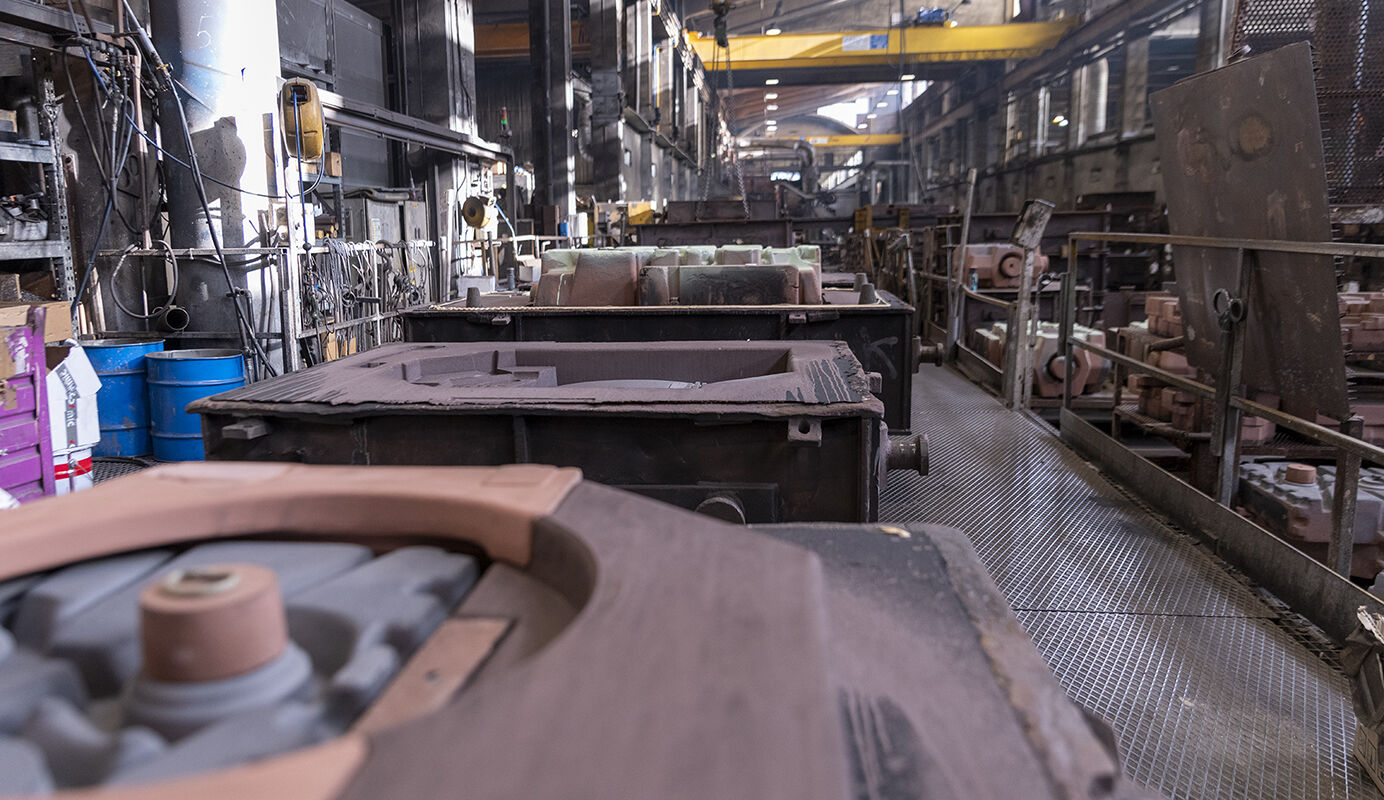

Schmelzanlage
Die Anlage wurde gemeinsam mit dem entsprechenden metallurgischen Verfahren von 2004 bis 2008 mit der Einführung von 2 Methangas-Oxyfuel-Drehrohröfen mit je 18 Tonnen und der Einführung des Sphäroguss-Herstellungsverfahrens mit Fülldraht komplett erneuert.
Das derzeitige Verfahren ermöglicht die Herstellung von Grauguss und Sphäroguss mit äußerster Flexibilität, insbesondere die Herstellung von Gusseisen hoher Qualität, das gegen niedrige Temperaturen beständig ist.
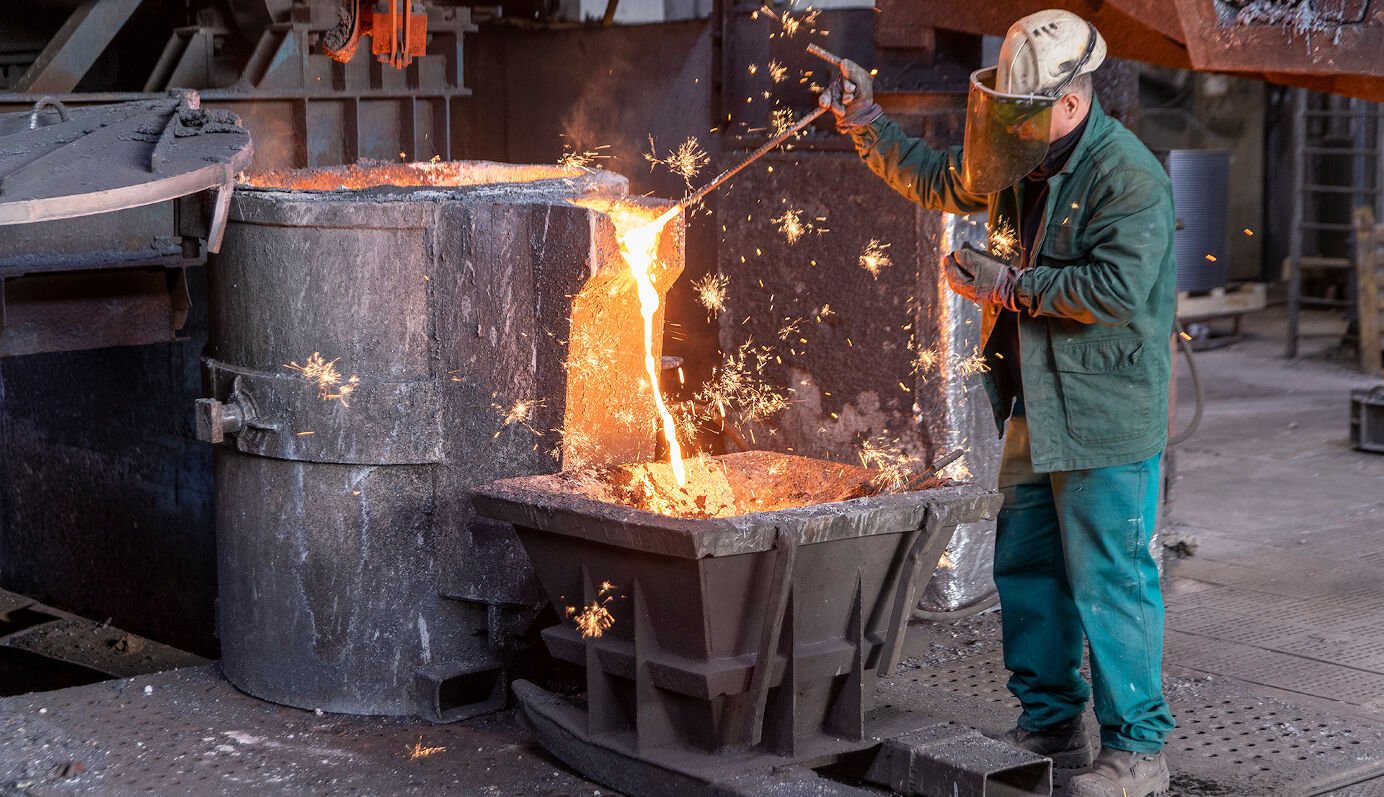
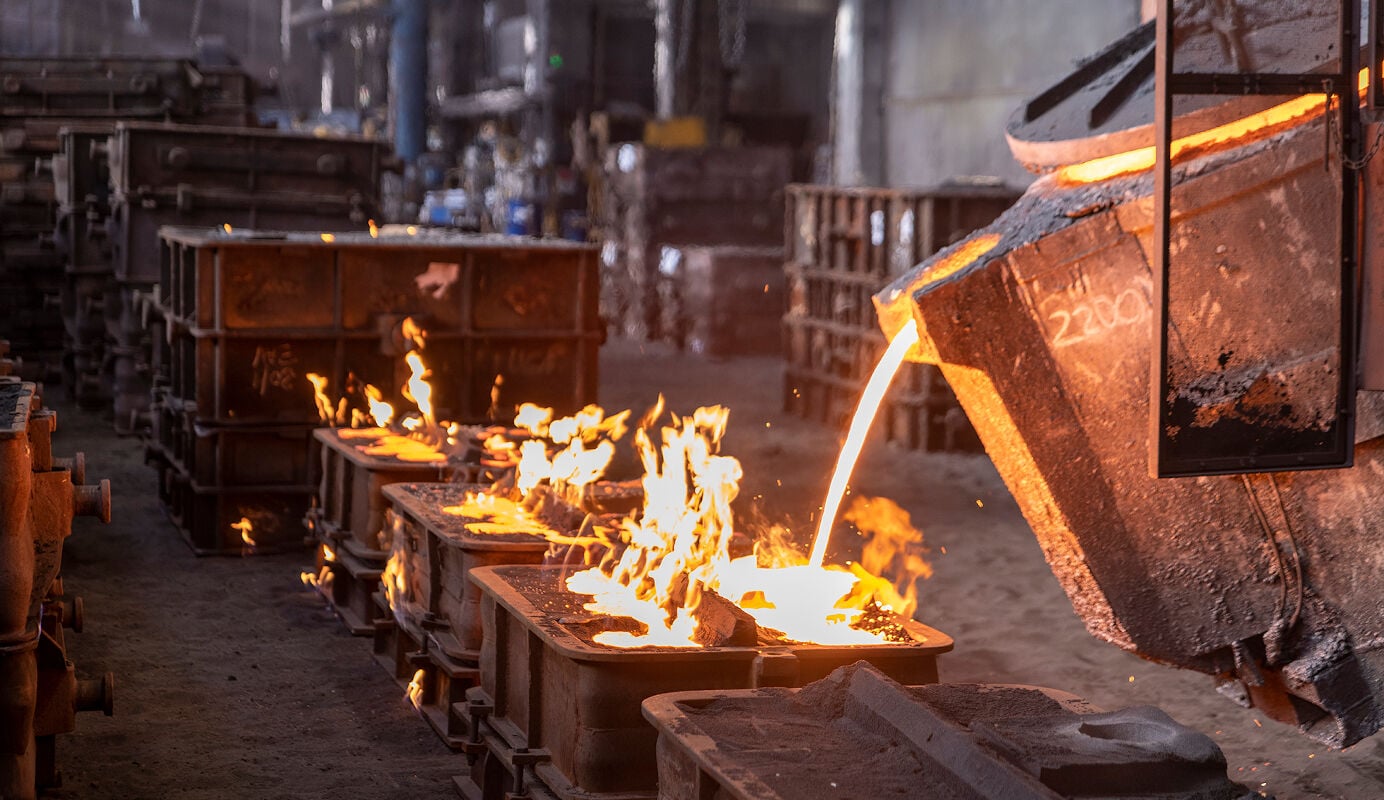
Das derzeitige metallurgische Verfahren ist aus energetischer und ökologischer Sicht äußerst effizient und erzeugt Emissionen, die keine NOx, SOx, CO und Dioxine enthalten, und Stäube, CO2 und Schlacken in lediglich geringem Umfang.
Die Kernproduktionsanlage besteht aus:
- 2 Mischern für die Herstellung von Kernen im manuellen Formverfahren mit Phenol-Furanharzen mit einem Gewicht zwischen 200 kg und 2.000 kg unter Verwendung von 100% regeneriertem Sand;
- 2 Maschinen H40 (Hansberg) mit Ashland-Verfahren;
- Eine automatische H25 und eine manuelle H12 mit Ashland-Verfahren;
- 3 Lackiertanks und ein Montagebereich.
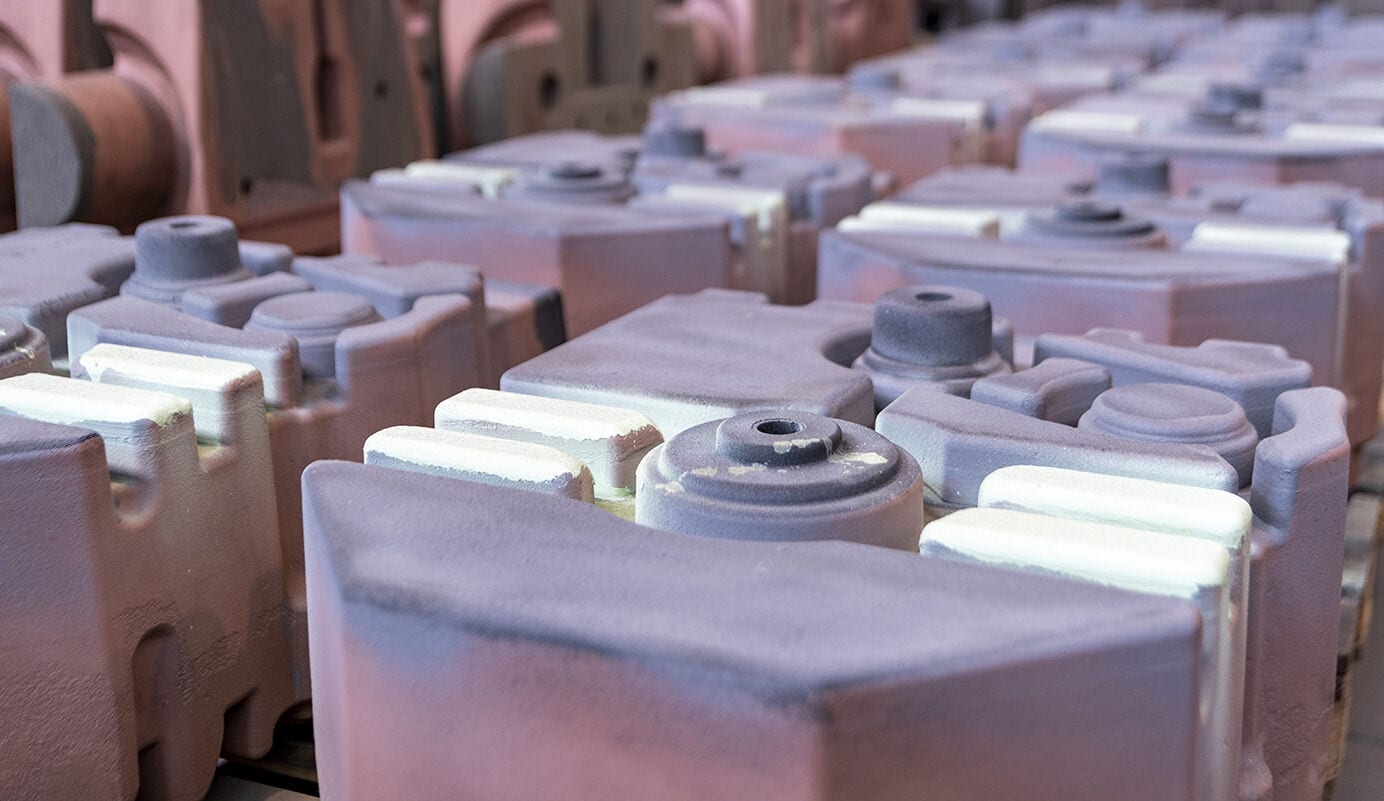
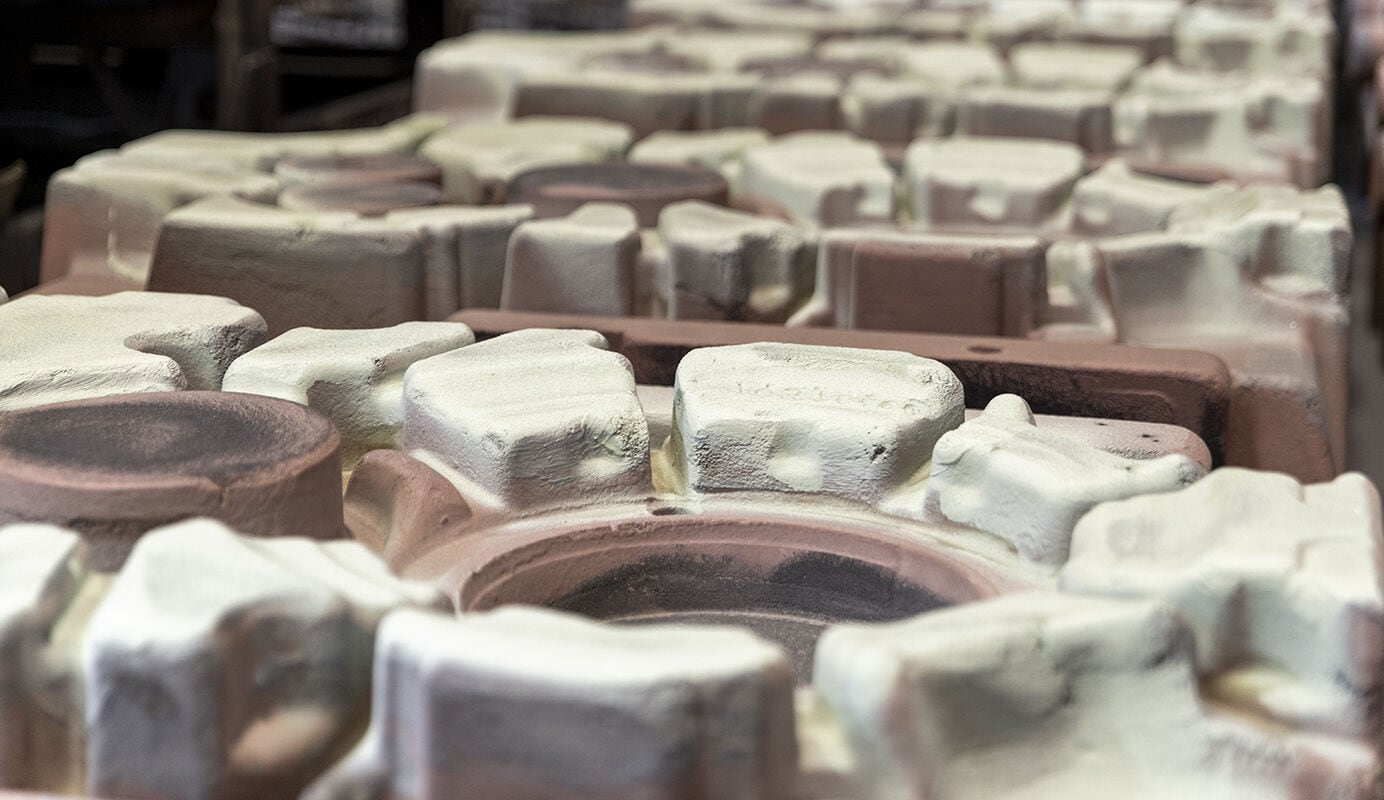
Die Kernproduktion deckt 95 % des Gewichts des Gesamtbedarfs der Gießerei ab. Dies stellt eine Garantie einer vollständigen Kontrolle des Produktionsprozesses von Gussteilen mit hohem technischem Anspruch dar, die sich durch eine starke Präsenz von Kernen mit komplexen Geometrien auszeichnen.
Das Unternehmen verfügt über zwei Wärmebehandlungsöfen für Dehnungs- und Ferritisierungsbehandlungen, die das metallurgische Verfahren vervollständigen:
- 1 Methanofen mit einer Kammer mit Abmessungen 8.000 x 1.500 x 1.500 mm;
- 1 Elektroofen mit einer Kammer mit Abmessungen 3.000 x 1.500 x 1.000 mm.